現在お買い物カゴには何も入っていません。
カメラプライヤー、またはカメラツールなど、色々な呼称で呼ばれるツールの紹介です。
弊社でハンドプライヤーを作るようになったきっかけはお客様からのご要望が何件か重なったためです。
精度の高く、強い製品を作れないか?
アマゾンで買えないサイズがあった。
市販のツールを一式まとめて購入しようとしたら買えなかった。
国産製品の安心した商品を希望
などのお声を頂き、以前にカメラメンテナンス関連のお客様からご依頼いただき特注で製作した実績も何度か有り、商品として設計・製作を開始いたしました。
作ってみて最初に思ったことは、対象物や市販品の精度です。
カメラのパーツの精度は恐ろしく出ていると思っていたのですが、確かに製品ごとには精度が高いパーツが使われておりますが、多種多様有り色々な規格が存在します。
例としてはライカさんなどはニコンさんと違うなどです。
よって、お客様が精度の出ている欲しいサイズが本当に存在しているかは?です。
そこで弊社では内径5.0mmから0.1mm単位で22.1mmまで取り揃えようと考えました。
しかし価格が高くなっては元も子も有りません。
ある程度の寸法はセット商品として量産し在庫を持つことにして価格を下げましたが、それ以外は特注にするしかない。
でも、価格を抑えた設計に特化して考えました。
もちろん、国産材料 で生産し RoHS2.0対応にした ものづくりです。
次に、素材について考えます。
市販品と呼べる製品は主に真鍮などで出来ています。
ちょうど良い粘りと引っ張り強さを求めたのか?切削性を求めたのかは分かりませんが良い選択だったと思います。
錆びなければ、、、
精度が必要な部分は真鍮では防錆効果を狙ったメッキなどのコーティングが難しいです。
その為、素材のままで使うことになります。
昨今のRoHS対応の影響で腐食に強い鉛やカドミが使えないため、腐食に弱くなりました。
ハンドツールでは鉛やカドミは論外ですが、昔は当然のように使われていました。
お客様より「使用後、手が汚れ臭くなる」・「ねじが変色した」とのお話を聞くまでは弊社も真鍮を選択しました。
(実際試作品で真鍮も試しました)
製作方法から企画して設計すると素材として真鍮は外れました。
次に試したのはステンレスです。
素材そのままでも腐食には強く、素材単価は上昇しますが加工性も良く、精度が出せます。ところが製品として欠点というか問題が見つかりました。
強すぎるのです。
実際、カメラメンテナンス業の会社様よりご依頼いただいた特注品はあくまで強さを求めて真鍮製からステンレス製に設計変更しました。
固着したねじを変形させながらも外す事ができました。
変形したねじは再製作が必要でしたが取れないとわからない部分もあったそうでした。
しかしながら個人のお客様はそうはいきません。(後々クレームが入るためです)
固着原因は接着剤の経年劣化による凝固が原因の場合と部品の腐食による膨張が考えられます。
対象物へキズを付けない様に工夫できないかを考えた時に一番、このツールで対象物へ負荷を与えている箇所に切削加工では出来ない微細なRをつけることが出来る放電加工を選択しました。
壊さないぎりぎりのラインを狙った素材で、、、と考えて
精度よく加工でき、ある程度強さが有り、製品価格を下げられる素材を求めた結果、アルミ A5052P で製作を決定し放電加工といった精度の高い加工方法を選択しています。
実際の加工精度は社内基準の0.03mmです。(次工程で0.01mm余裕を見ています)
仕上げ方法もバレル研磨を行い、コンパウンドを調整し腐食にもある程度の強さを出せるようになりました。
弊社のアルミ製ハンドプライヤ(厚さ3mm)はこうして作られるようになりました。
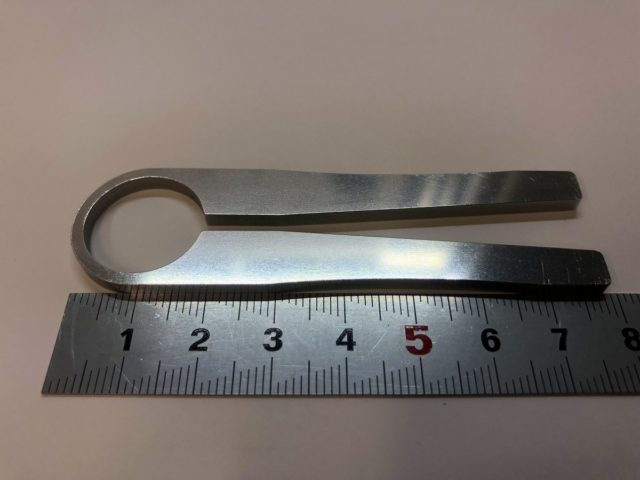
もちろん、強さを求めたステンレス製(厚さ2.5mm)も販売しております。
ステンレス2.5mmで製作
価格などは下記ページでご覧ください。
企画・設計・製作は 若井製作所 で行っております。